Share
SALT LAKE CITY — Scott Sabin knows as well as anyone that working inside a hectic and high-stakes hospital environment every day has a special way of focusing the mind.
“High expectations and complex work are a commonplace part of the regular workflow,” said Sabin, a project manager with Jacobsen Construction Company. “Very quickly you learn to be intensely aware of your surroundings, and how your work is affecting those around you.”
For Sabin, being strictly organized and staying relentlessly focused has been a part of his job description for nearly 11 years at Primary Children’s Hospital. He is responsible for continually pushing back against unpredictability by planning for every contingency and maneuvering around every complexity at the ever-busy and essential facility. Jacobsen has been reshaping and modernizing Primary Children’s, the most advanced pediatric hospital in the Intermountain West, on a continual basis for the past 15-plus years — having renovated more than 75% of its total space during that period.
“The work is demanding. And even though I am aware of everything that rides on working safely and effectively in such a sensitive space, it would not do me any good to be intimidated by the magnitude of that responsibility,” Sabin said. “I have learned to enjoy the process of rising to the challenge.”
The latest intriguing challenge facing Sabin and his team at Primary Children’s Hospital is the construction of a Hybrid Operating Room, a highly sophisticated surgery suite that employs the use of 3D imaging technology in real time to help physicians provide precise care during important medical procedures. Located at the heart of the hospital on the second floor, the Hybrid Operating Room began construction in April and will be completed in October of 2022. It will be capable of hosting neurosurgery, liver surgery, vascular surgery, cardiac surgery, and orthopedic and trauma surgery. Among other features, the room will include:
- a high-tech “C arm” imaging apparatus that can be nimbly maneuvered to obtain numerous types of useful images of the patient
- a leading-edge patient bed design
- enormous display screens helping surgeons see their work up close
- a large behind-glass control room capable of displaying detailed real-time imaging results and surgery data for use by several support team medical professionals at any given time
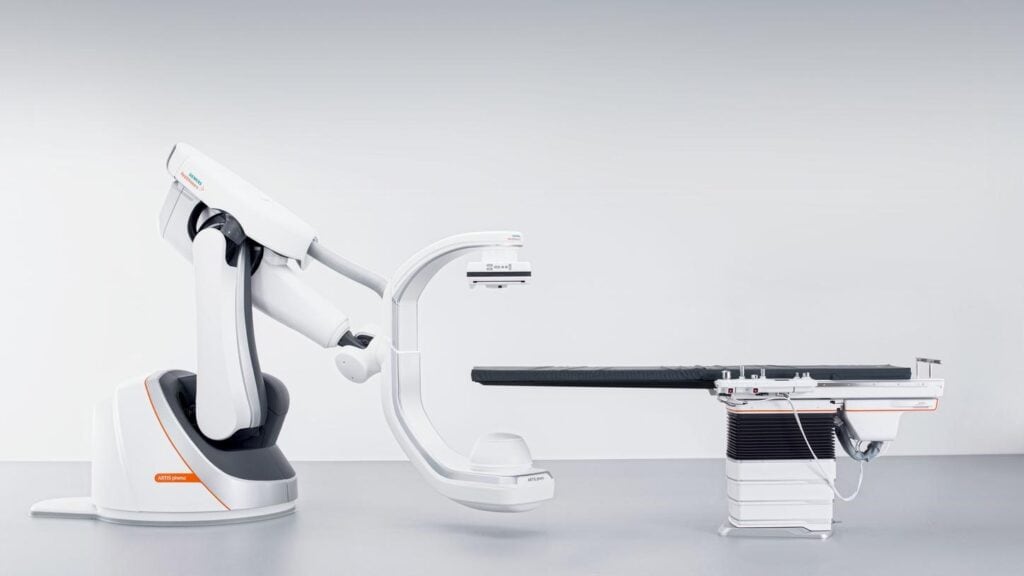
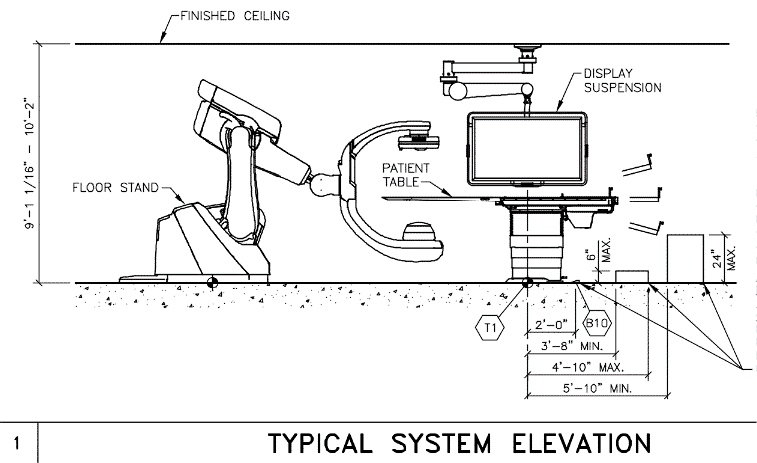
Because it is in a central location situated between 13 currently active operating rooms, gaining adequate access to the construction site without disrupting the continuity and safety of vital pediatric surgeries has required the project team to find innovative solutions that are at once both dazzlingly creative and stringently safe and reliable.
“Even working in an active hospital for as long as I have, this project stands out for how many layers of patient safety preservation must be accounted for,” Sabin said. “Putting our heads together to find strategies that will work has really put our team’s skills to the test.”
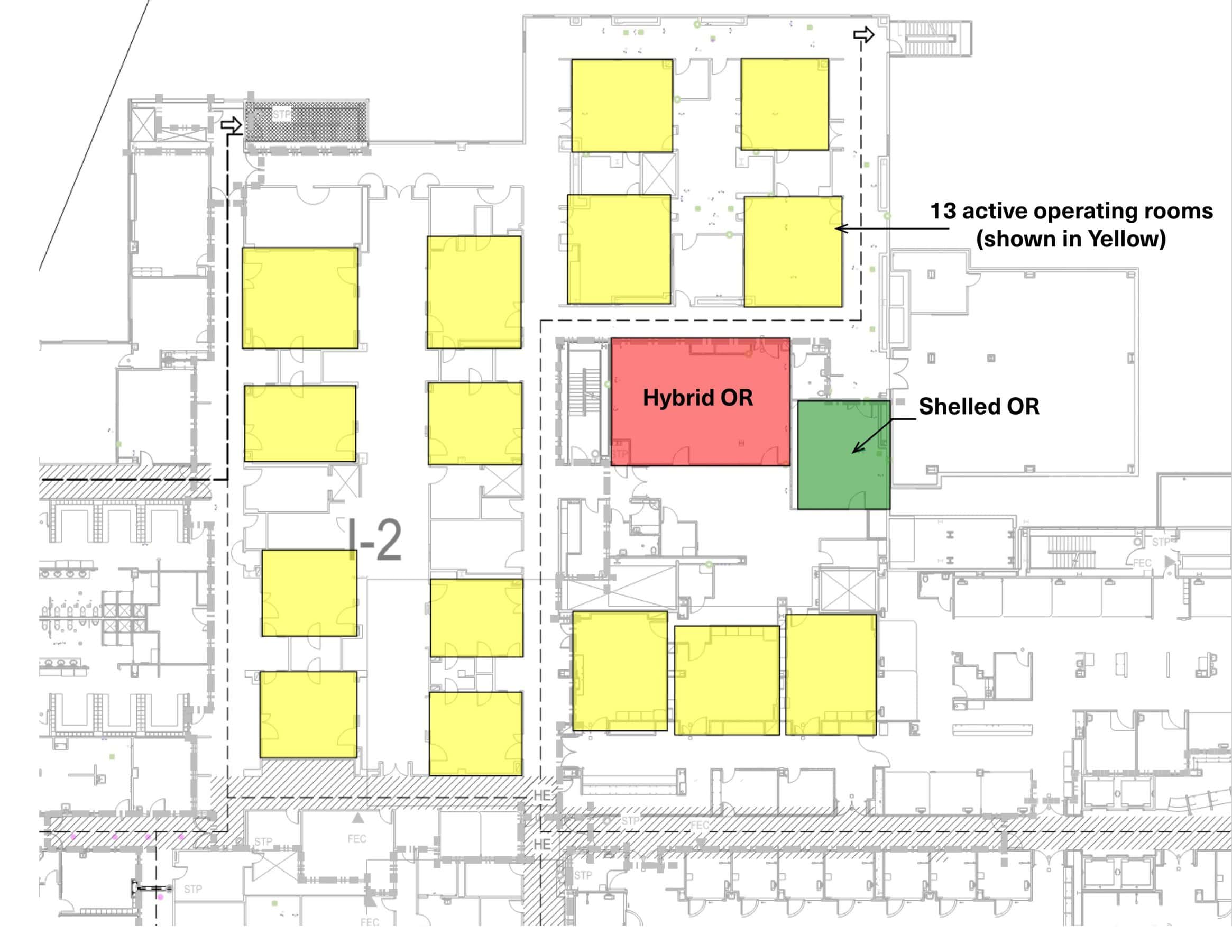
Before making space for craft workers to navigate their way in and out of the room, Sabin and the project’s design and engineering leaders first had to take into account the exceedingly strict infection prevention protocols observed by the hospital in order to protect surgery patients. Namely, the sterile core hospital space between all the operating rooms, which would need to be passed through to access the construction site, only grants access to individuals who are fully gowned-up from head to toe in Tyvek “bunny suit” coveralls.
“Doing this for every task on the project from start to finish wouldn’t be realistic or practical, because it would require de-gowning and re-gowning every time someone needed to retrieve a tool, use the restroom or leave the work site for any reason,” Sabin said.
To work around this limitation, the project team decided to install a well-sealed, infection-protected tunnel corridor running from the exterior of the hospital directly into the inside of the Hybrid Operating Room work site. There wasn’t an existing exit on the exterior of the building that would naturally work as one end of the tunnel, so workers removed the metal-panel wall on the building’s exterior in a pre-selected location to wholly create the tunnel endpoint from scratch. A stairway and supportive scaffolding were put into place on the outside of the building to help workers access the tunnel.
“While certainly unusual, this newly created pathway between the Hybrid Operating Room and the exterior of the hospital is what puts our project team members in the best possible position to do quality work while meeting ambitious budget and schedule expectations,” Sabin said.
Making room for a worker access tunnel also required the rerouting of several crucial gas supply lines that are used in operating rooms. These lines, which directly supply gases such as nitrous oxide, nitrogen, carbon dioxide, oxygen and more to patients in surgery, were rapidly relocated during off hours in order to prevent impacts to patients. Reconnection of the lines needed to be completed quickly — but also accurately — to ensure patient safety and hospital continuity.
“Re-connecting any of these gas lines incorrectly would be catastrophically dangerous for patients in surgery, so we included several real-time redundancies to ensure all of the lines were hooked up to the correctly identified gas source,” Sabin said. “Although we moved fast, every part of the process was very deliberate and detailed in order to ensure there could be total confidence in the accuracy of the result. This required a lot of advance planning before the task was set into motion.”
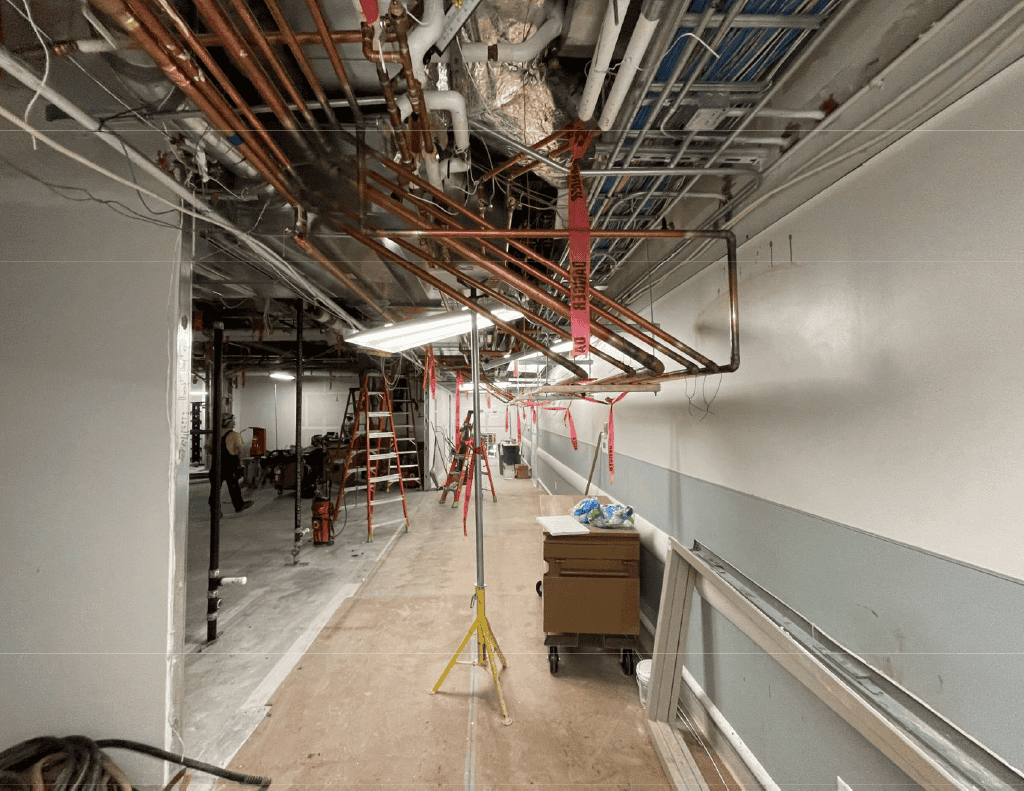
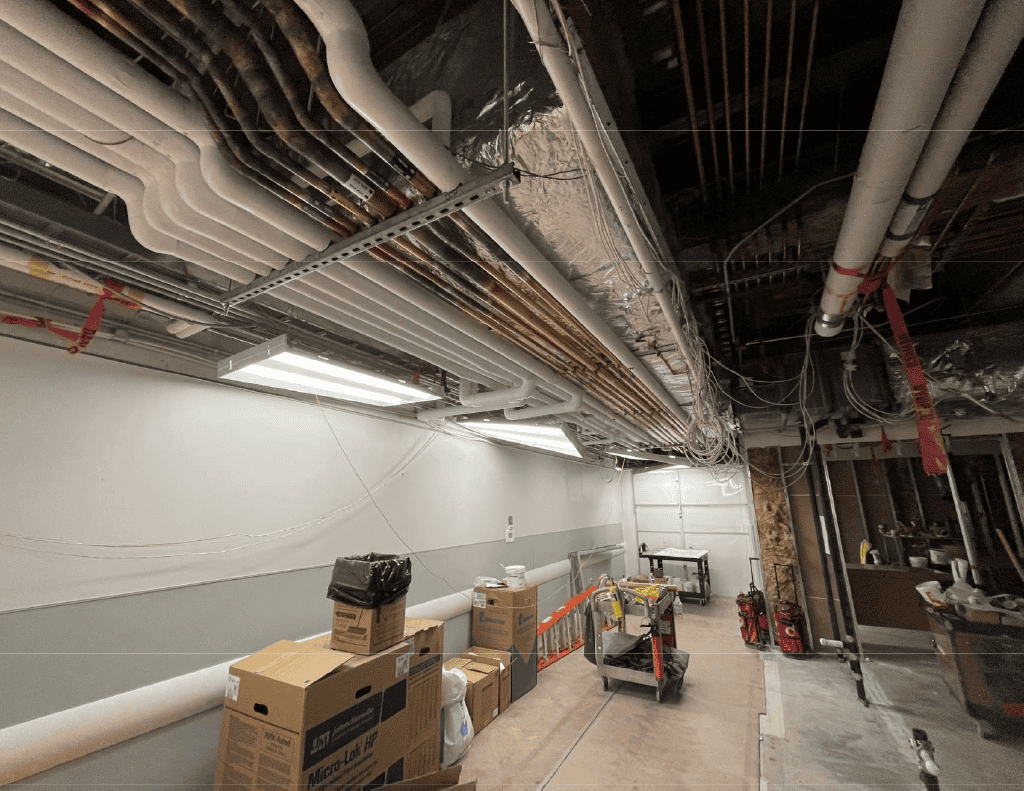
Because the project would also require structural steel reinforcement inside the enclosed ceiling of the level below in order to provide better weight-bearing support for the 8,910-pound operating room equipment, a strategy was devised to likewise avoid disruptions to the histology lab located beneath the Hybrid Operating Room space.
“The histology lab plays an essential role in deep-freezing, very finely slicing, and closely examining body tissue samples to help with making accurate diagnoses, so it was not a feasible option to close the lab and relocate its elaborate, finely-calibrated equipment to another space in the hospital,” Sabin said.
Instead, the lab’s functionality was preserved by using a scaffolding dance floor with a very high platform just 12 inches below the ceiling. The scaffolding dance floor was located high enough that lab employees were not blocked off from using any of their vital workspace.
Protective netting was carefully installed above the entire histology space to prevent any dust or other debris related to the ceiling work from landing in the lab, in order to help preserve its carefully maintained sterility. Working in extremely tight spaces, the project team was then able to remove portions of the ceiling finishes and interior, creating a couple feet of additional vertical space in which to work — although the space is still relatively confined. In this tightly constrained above-ceiling environment, workers are now able to add structural steel to the weight-bearing floor above, helping it support the enormously heavy Hybrid Operating Room equipment.
“It’s pretty fun that instead of bringing in stilts for ceiling work like usual, the crews have had to bring knee pads to help them crawl,” Sabin said.
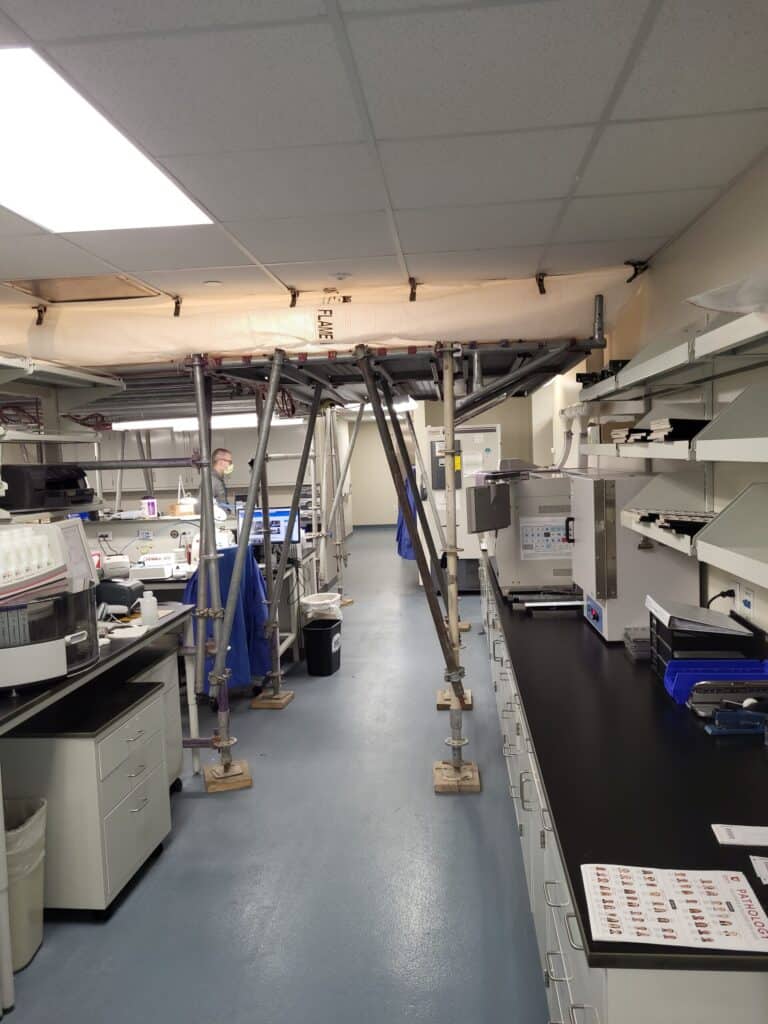
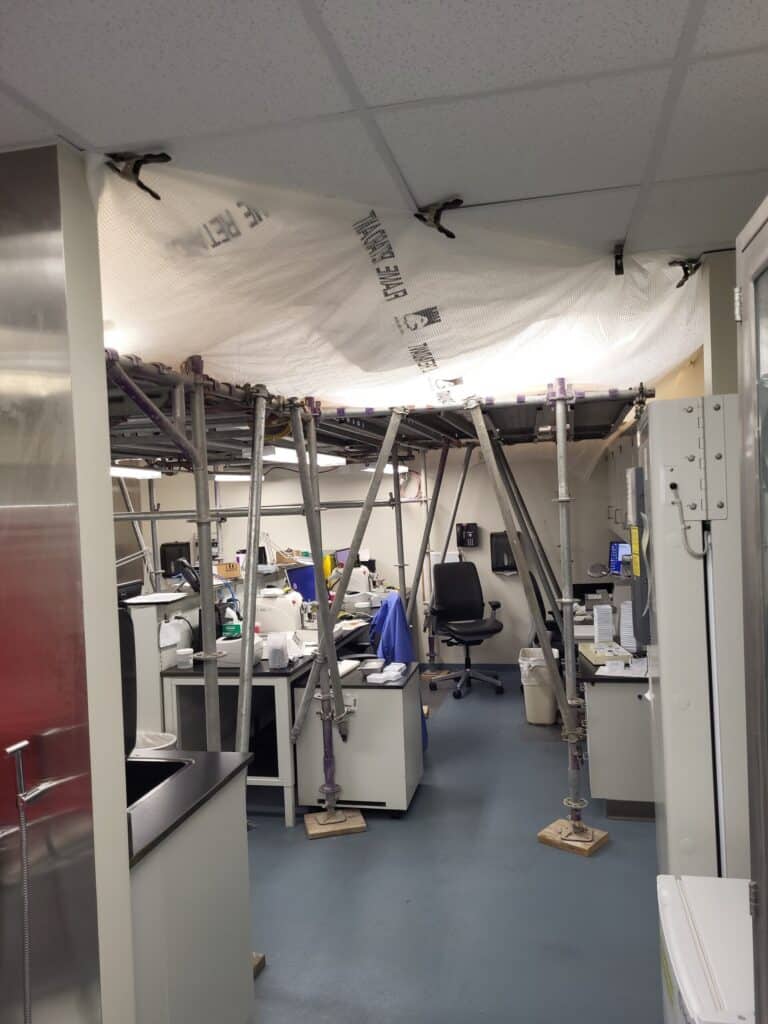
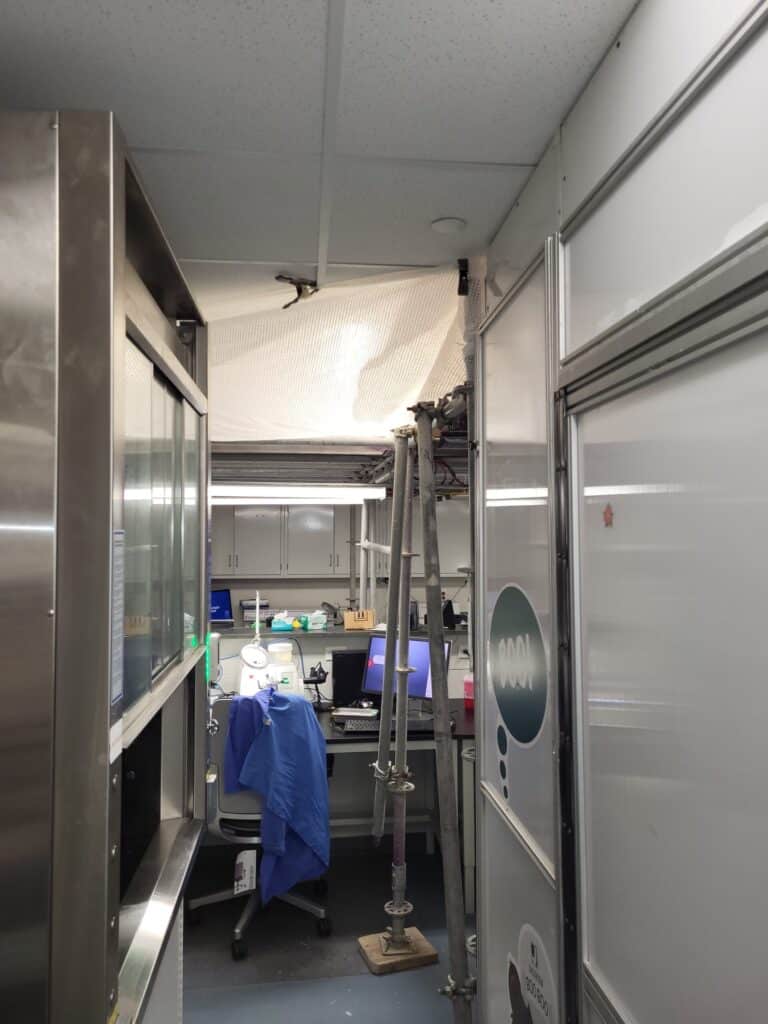
An intricate cable management conduit system is also being installed as part of the work done in the ceiling space; this system is built to reliably connect power to an extensive range of important electrical, computer and medical systems in the Hybrid Operating Room while also keeping the many cables orderly and distinguishable from one another.
While the tunnel created for workers eliminates the need for wearing a full infection-control bodysuit on the large majority of tasks on the project, there are some exceptions. For example, deliveries of very heavy and bulky medical equipment are taken through the sterile core area between operating rooms, which provides a larger opening for the arriving equipment than the temporary tunnel is capable of. To fully comply with anti-infection protocols, all workers are fully suited-up for the delivery and the equipment is wiped down with powerful disinfectants immediately before entering the sensitive space.
“Regardless of the specific anti-infection strategy on a given task, the goal is always to follow the hospital’s standards as carefully and comprehensively as possible,” Sabin said. “With a little bit of ingenuity and a lot of collaboration with facilities managers, engineers and designers on this project, it’s remarkable how many flexible solutions we can identify. It’s gratifying to know that we’re capable of helping the surgery teams take a big technological leap forward into the future while also faithfully safeguarding the physical environment and overall wellbeing of young patients who need the best of what the hospital can offer today.”